Magnetic Permeability < 1.002 | Name Nickel titanium | |
![]() | ||
Density 6.45 g/cm (0.233 lb/cu in) | ||
Electrical Resistivity (Austenite) Coefficient of Thermal Expansion (Austenite) Magnetic Susceptibility (Austenite) emu/g Thermal Conductivity (Austenite) 0.18 W/cm·K |
The qualities of superelastic and heat activated nickel titanium wires
Nickel titanium, also known as Nitinol (part of shape memory alloy), is a metal alloy of nickel and titanium, where the two elements are present in roughly equal atomic percentages e.g. Nitinol 55, Nitinol 60.
Contents
- The qualities of superelastic and heat activated nickel titanium wires
- magic memory metal nickel titanium or nitinol wire
- History
- Mechanism
- Manufacturing process
- Challenges
- Applications
- Thermal and electrical actuators
- Biocompatible and biomedical applications
- Damping systems in structural engineering
- Other applications and prototypes
- References
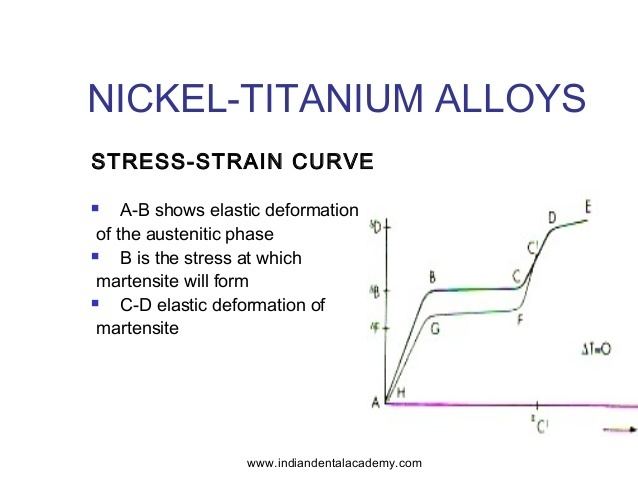
Nitinol alloys exhibit two closely related and unique properties: shape memory effect (SME) and superelasticity (SE; also called pseudoelasticity, PE). Shape memory is the ability of nitinol to undergo deformation at one temperature, then recover its original, undeformed shape upon heating above its "transformation temperature". Superelasticity occurs at a narrow temperature range just above its transformation temperature; in this case, no heating is necessary to cause the undeformed shape to recover, and the material exhibits enormous elasticity, some 10-30 times that of ordinary metal.
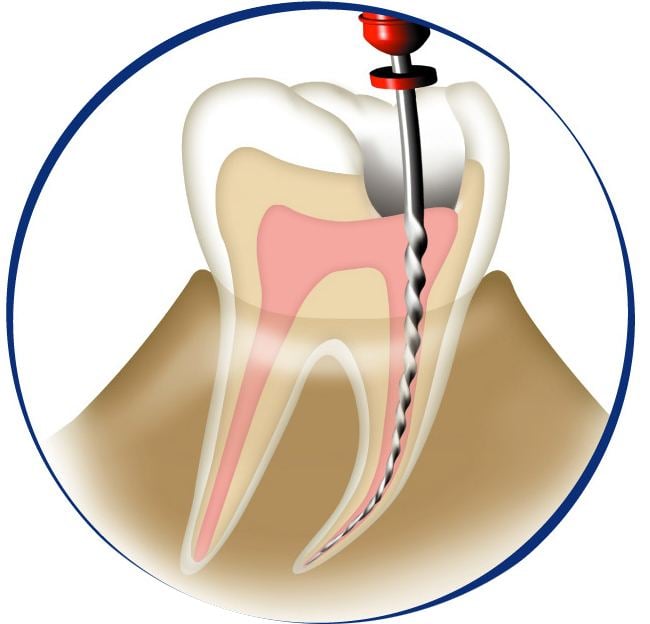
magic memory metal nickel titanium or nitinol wire
History
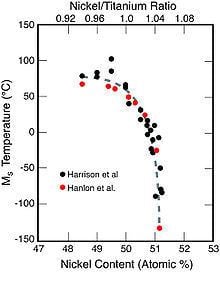
The word Nitinol is derived from its composition and its place of discovery: (Nickel Titanium-Naval Ordnance Laboratory). William J. Buehler along with Frederick Wang, discovered its properties during research at the Naval Ordnance Laboratory in 1959. Buehler was attempting to make a better missile nose cone, which could resist fatigue, heat and the force of impact. Having found that a 1:1 alloy of nickel and titanium could do the job, in 1961 he presented a sample at a laboratory management meeting. The sample, folded up like an accordion, was passed around and flexed by the participants. One of them applied heat from his pipe lighter to the sample and, to everyone's surprise, the accordion-shaped strip stretched and took its previous shape.
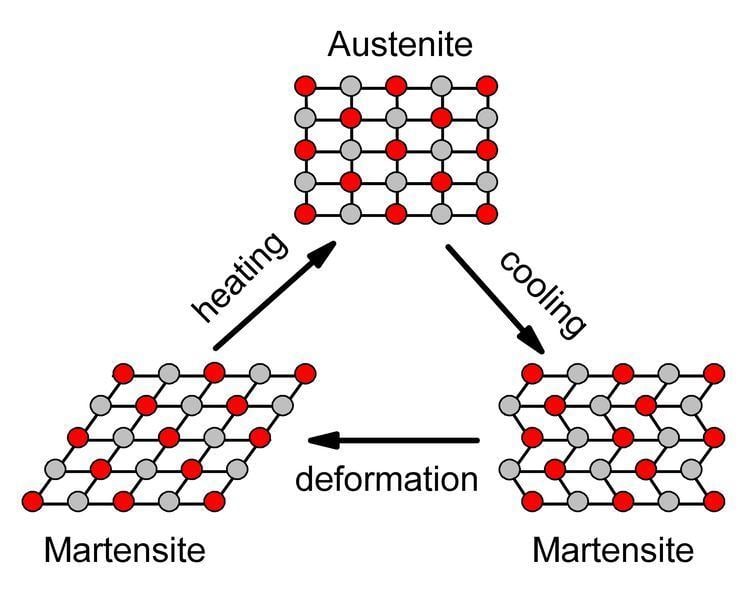
While the potential applications for nitinol were realized immediately, practical efforts to commercialize the alloy did not take place until a decade later. This delay was largely because of the extraordinary difficulty of melting, processing and machining the alloy. Even these efforts encountered financial challenges that were not readily overcome until the 1980s, when these practical difficulties finally began to be resolved.
The discovery of the shape-memory effect in general dates back to 1932, when Swedish chemist Arne Ölander first observed the property in gold-cadmium alloys. The same effect was observed in Cu-Zn (brass) in the early 1950s.
Mechanism
Nitinol's unusual properties are derived from a reversible solid-state phase transformation known as a martensitic transformation, between two different martensite crystal phases, requiring 10,000–20,000 psi (69–138 MPa) of mechanical stress.
At high temperatures, nitinol assumes an interpenetrating simple cubic structure referred to as austenite (also known as the parent phase). At low temperatures, nitinol spontaneously transforms to a more complicated monoclinic crystal structure known as martensite (daughter phase). There are four transition temperatures associated to the austenite-to-martensite and martensite-to-austenite transformations. Starting from full austenite, martensite begins to form as the alloy is cooled to the so-called martensite start temperature, or Ms, and the temperature at which the transformation is complete is called the martensite finish temperature, or Mf. When the alloy is fully martensite and is subjected to heating, austenite starts to form at the austenite start temperature, As, and finishes at the austenite finish temperature, Af.
The cooling/heating cycle shows thermal hysteresis. The hysteresis width depends on the precise nitinol composition and processing. Its typical value is a temperature range spanning about 20-50 K (20-50 °C; 36-90 °F) but it can be reduced or amplified by alloying and processing.
Crucial to nitinol properties are two key aspects of this phase transformation. First is that the transformation is "reversible", meaning that heating above the transformation temperature will revert the crystal structure to the simpler austenite phase. The second key point is that the transformation in both directions is instantaneous.
Martensite's crystal structure (known as a monoclinic, or B19' structure) has the unique ability to undergo limited deformation in some ways without breaking atomic bonds. This type of deformation is known as twinning, which consists of the rearrangement of atomic planes without causing slip, or permanent deformation. It is able to undergo about 6–8% strain in this manner. When martensite is reverted to austenite by heating, the original austenitic structure is restored, regardless of whether the martensite phase was deformed. Thus the name "shape memory" refers to the fact that the shape of the high temperature austenite phase is "remembered," even though the alloy is severely deformed at a lower temperature.
A great deal of pressure can be produced by preventing the reversion of deformed martensite to austenite — from 35,000 psi to, in many cases, more than 100,000 psi (689 MPa). One of the reasons that nitinol works so hard to return to its original shape is that it is not just an ordinary metal alloy, but what is known as an intermetallic compound. In an ordinary alloy, the constituents are randomly positioned in the crystal lattice; in an ordered intermetallic compound, the atoms (in this case, nickel and titanium) have very specific locations in the lattice. The fact that nitinol is an intermetallic is largely responsible for the complexity in fabricating devices made from the alloy.
The scenario described above (cooling austenite to form martensite, deforming the martensite, then heating to revert to austenite, thus returning the original, undeformed shape) is known as the thermal shape memory effect. To fix the original "parent shape," the alloy must be held in position and heated to about 500 °C (932 °F). This process is usually called shape setting. A second effect, called superelasticity or pseudoelasticity, is also observed in nitinol. This effect is the direct result of the fact that martensite can be formed by applying a stress as well as by cooling. Thus in a certain temperature range, one can apply a stress to austenite, causing martensite to form while at the same time changing shape. In this case, as soon as the stress is removed, the nitinol will spontaneously return to its original shape. In this mode of use, nitinol behaves like a super spring, possessing an elastic range 10–30 times greater than that of a normal spring material. There are, however, constraints: the effect is only observed about 0-40 K (0-40 °C; 0-72 °F) above the Af temperature. This upper limit is referred to as Md, which corresponds to the highest temperature in which it is still possible to stress-induce the formation of martensite. Below Md, martensite formation under load allows superelasticity due to twinning. Above Md, since martensite is no longer formed, the only response to stress is slip of the austenitic microstructure, and thus permanent deformation.
Nitinol is typically composed of approximately 50 to 51% nickel by atomic percent (55 to 56% weight percent). Making small changes in the composition can change the transition temperature of the alloy significantly. Transformation temperatures in nitinol can be controlled to some extent, where Af temperature ranges from about −20 °C to +110 °C. Thus, it is common practice to refer to a nitinol formulation as "superelastic" or "austenitic" if Af is lower than a reference temperature, while as "shape memory" or "martensitic" if higher. The reference temperature is usually defined as the room temperature or the human body temperature (37 °C; 98 °F).
One often-encountered effect regarding nitinol is the so-called R-phase. The R-phase is another martensitic phase that competes with the martensite phase mentioned above. Because it does not offer the large memory effects of the martensite phase, it is usually of non practical use.
Manufacturing process
Nitinol is exceedingly difficult to make, due to the exceptionally tight compositional control required, and the tremendous reactivity of titanium. Every atom of titanium that combines with oxygen or carbon is an atom that is robbed from the NiTi lattice, thus shifting the composition and making the transformation temperature that much lower. There are two primary melting methods used today:
While both methods have advantages, it has been demonstrated that an industrial state-of-the-art VIM melted material has smaller inclusions than an industrial state-of-the-art VAR one, leading to a higher fatigue resistance. Other research report that VAR employing extreme high-purity raw materials may lead to a reduced number of inclusions and thus to an improved fatigue behavior. Other methods are also used on a boutique scale, including plasma arc melting, induction skull melting, and e-beam melting. Physical vapour deposition is also used on a laboratory scale.
Hot working of nitinol is relatively easy, but cold working is difficult because the enormous elasticity of the alloy increases die or roll contact, leading to tremendous frictional resistance and tool wear. For similar reasons, machining is extremely difficult—to make things worse, the thermal conductivity of nitinol is poor, so heat is difficult to be removed. Grinding (abrasive cutting), Electrical discharge machining (EDM) and laser cutting are all relatively easy.
Heat treating nitinol is delicate and critical. It is the knowledge intensive process to fine-tune the transformation temperatures. Aging time and temperature controls the precipitation of various Ni-rich phases, and thus controls how much nickel resides in the NiTi lattice; by depleting the matrix of nickel, aging increases the transformation temperature. The combination of heat treatment and cold working is essential in controlling the properties of nitinol products.
Challenges
Fatigue failures of nitinol devices are a constant subject of discussion. Because it is the material of choice for applications requiring enormous flexibility and motion (e.g., peripheral stents, heart valves, smart thermomechanical actuators and electromechanical microactuators), it is necessarily exposed to much greater fatigue strains compared to other metals. While the strain-controlled fatigue performance of nitinol is superior to all other known metals, fatigue failures have been observed in the most demanding applications. There is a great deal of effort underway trying to better understand and define the durability limits of nitinol.
Nitinol is half nickel, and thus there has been a great deal of concern in the medical industry regarding the release of nickel, a known allergen and possible carcinogen. (Nickel is also present in substantial amounts in stainless steel and cobalt-chrome alloys.) When properly treated (via electropolishing and/or passivation), nitinol forms a very stable protective TiO2 layer that acts as a very effective and self-healing barrier against ion exchange. It has been repeatedly shown that nitinol releases nickel at a slower pace than stainless steel, for example. With that said, very early medical devices were made without electropolishing, and corrosion was observed. Today's nitinol vascular self-expandable metallic stents, for example, show no evidence of corrosion or nickel release, and the outcomes in patients with and without nickel allergies are indistinguishable.
There are constant and long-running discussions regarding inclusions in nitinol, both TiC and Ti2NiOx. As in all other metals and alloys, inclusions can be found in Nitinol. The size, distribution and type of inclusions can be controlled to some extent. Theoretically, smaller, rounder and few inclusions should lead to increased fatigue durability. In literature, some early works report to have failed to show measurable differences, while novel studies demonstrate a dependence of fatigue resistance on the typical inclusion size in an alloy.
Nitinol is difficult to weld, both to itself and other materials. Laser welding nitinol to itself is a relatively routine process. More recently, strong joints between NiTi wires and stainless steel wires have been made using nickel filler. Laser and Tungsten Inert Gas (TIG) welds have been made between NiTi tubes and stainless steel tubes . More research is ongoing into other processes and other metals to which nitinol can be welded.
Actuation frequency of nitinol is dependent on the heat management, especially during the cooling phase. Numerous methods are used to increase the cooling performance, such as forced air, flowing liquids, thermoelectric modules (i.e. Peltier or semiconductor heat pumps), heat sinks, conductive materials and higher surface-to-volume ratio (improvements up to 3.3 Hz with very thin wires and up to 100 Hz with thinfilm nitinol). The fastest nitinol actuation recorded was carried by a high voltage capacitor discharge which heated an SMA wire in a manner of microseconds, and resulted in a complete phase transformation (and high velocities) in a few milliseconds.
Recent advances have shown that processing of nitinol can expand thermomechanical capabilities, allowing for multiple shape memories to be embedded within a monolithic structure. Research on multi-memory technology is on-going and promises to deliver enhanced shape memory devices in the near future , and the application of new materials and material structures, such hybrid shape memory materials (SMMs) and shape memory composites (SMCs).
Applications
There are four commonly used types of applications for nitinol:
Free recovery
Nitinol is deformed at a low temperature, and heated to recover its original shape through the Shape Memory effect.Constrained recovery
As for free recovery, except that recovery is rigidly prevented and thus a stress is generated.Work production
Here the alloy is allowed to recover, but to do so it must act against a force (thus doing work).Superelasticity
Nitinol acts as a super spring through the Superelastic effect.In 1989 a survey was conducted in the United States and Canada that involved seven organizations. The survey focused on predicting the future technology, market, and applications of SMAs. The companies predicted the following uses of nitinol in a decreasing order of importance: (1) Couplings, (2) Biomedical and medical, (3) Toys, demonstration, novelty items, (4) Actuators, (5) Heat Engines, (6) Sensors, (7) Cryogenically activated die and bubble memory sockets, and finally (8) lifting devices.
Today, nitinol finds application in the listed industrial applications: